Предпосылки построения единой информационной системы
«Сегодня огромная проблема в экономике России — это низкая производительность труда, — начал беседу Анатолий Морозов, директор завода «Ремит». — Многие до сих считают, что повышение производительности труда достижимо только увеличением числа работников. Но это мнение ошибочно. На самом деле для повышения производительности необходимо организовывать процессы на производстве путем их стандартизации».
Действительно, рынок постоянно выдвигает новые условия работы, внешняя среда очень быстро меняется. Оперативно принимать правильные решения можно только на основе точной и актуальной информации. Получать же такую информацию можно лишь на основе хорошей информационной системы.
Важной предпосылкой построения новой ИТ-системы стал и тот факт, что за последние 10 лет качественно поменялся менеджмент компании, пришли новые молодые грамотные специалисты, которые поддержали идею построения единой информационной системы. Они-то и вошли в команду по внедрению. Причем часть из них уже имела опыт работы с информационными, в том числе и западными, системами.
Выбор решения
«Мы отдали предпочтение системе «1С:ERP Управление предприятием 2.0», — поясняет Евгений Голубцов, — потому что этот продукт дал нам всем свободу как в выборе решений на его основе, так и в разработках». Существенную роль в выборе системы сыграли партнеры «Ремит» — компания «Абсолют Софт», которые убедили заказчика, что система «1С:ERP Управление предприятием 2.0» сможет решить их задачи.
Ключевую роль в выборе сыграли комплексность и гибкость системы. «Западную систему, к сожалению, гораздо сложнее подстроить под требования предприятия», — продолжил Евгений Голубцов, директор по ИТ завода «Ремит». Например, на заводе есть участок по составлению специй. И на то чтобы подстроить систему под специфику производства «Ремит» и автоматизировать этот участок, у проектной команды ушло всего два дня. Это характерный пример того, как на отдельно взятом участке можно быстро адаптировать систему под специфику предприятия.
Ход проекта
Проект был начат в августе 2014 года и завершен в июне 2015 года. Его особенностью стал тот факт, что не составлялось объемное детальное ТЗ. Команда проекта отлично знала что необходимо делать и было решено отказаться от составления и согласования детального ТЗ для ускорения хода проекта.
В ноябре 2014 года стартовал проект по разработке и настройкам в системе. Внедрение «1С:ERP Управление предприятием 2.0» очень сильно отличается от внедрения других программных продуктов фирмы «1С». Большая часть специфических задач решается настройками, а не доработками. Работы велись быстро, бухгалтерия приступила к работе в новой системе через два месяца со дня запуска проекта. С января 2015 года в новой системе уже начали работать бухгалтерия, расчеты с банком и учет основных средств.
Пока настраивалась типовая система «1С:ERP Управление предприятием 2.0», на заводе провели инвентаризацию, подготовили нормативно-справочную информацию, осуществили перенос данных в новую систему. Обучение начали с бухгалтерии и проводили его по классической схеме через ключевых пользователей. А в области производства упор был сделан на интуитивно-понятный интерфейс, который не потребует обучения.
«При разработке интерфейса мы лично стояли на рабочих местах, — вспоминает Евгений Голубцов, — и определяли, где и какую кнопку надо разместить. Сначала это были эскизы, чтобы кнопки были на уровне глаз, сформированы в понятном порядке. Одним словом, стремились сделать дружественный интерфейс подобно терминалам QIWI. В результате такого подхода нам даже не пришлось писать инструкции — просто проводили первичный инструктаж».
Основным фактором успеха стала инициация и поддержка проекта генеральным директором, а также участие группы молодых и, что самое главное, опытных менеджеров.
Учет продукции по сериям
Руководству «Ремит» было важно чувствовать управляемость бизнеса, иметь реальную картину по производству, а также точные сведения об остатках. Ключевой элемент новой информационной системы — учет продукции по сериям. Для пищевого предприятия, которым является «Ремит», это очень важно, ведь внутрипроизводственная прослеживаемость создания продукта и происхождения сырья и ингредиентов, из которых создан продукт, — это одно из важнейших требований пищевых стандартов. Прослеживание продукции начинается от ее поступления от поставщика и через все этапы до упаковки готовой продукции. На настоящий момент система успешно прошла ряд аудитов, в том числе и со стороны клиентов «Ремит».
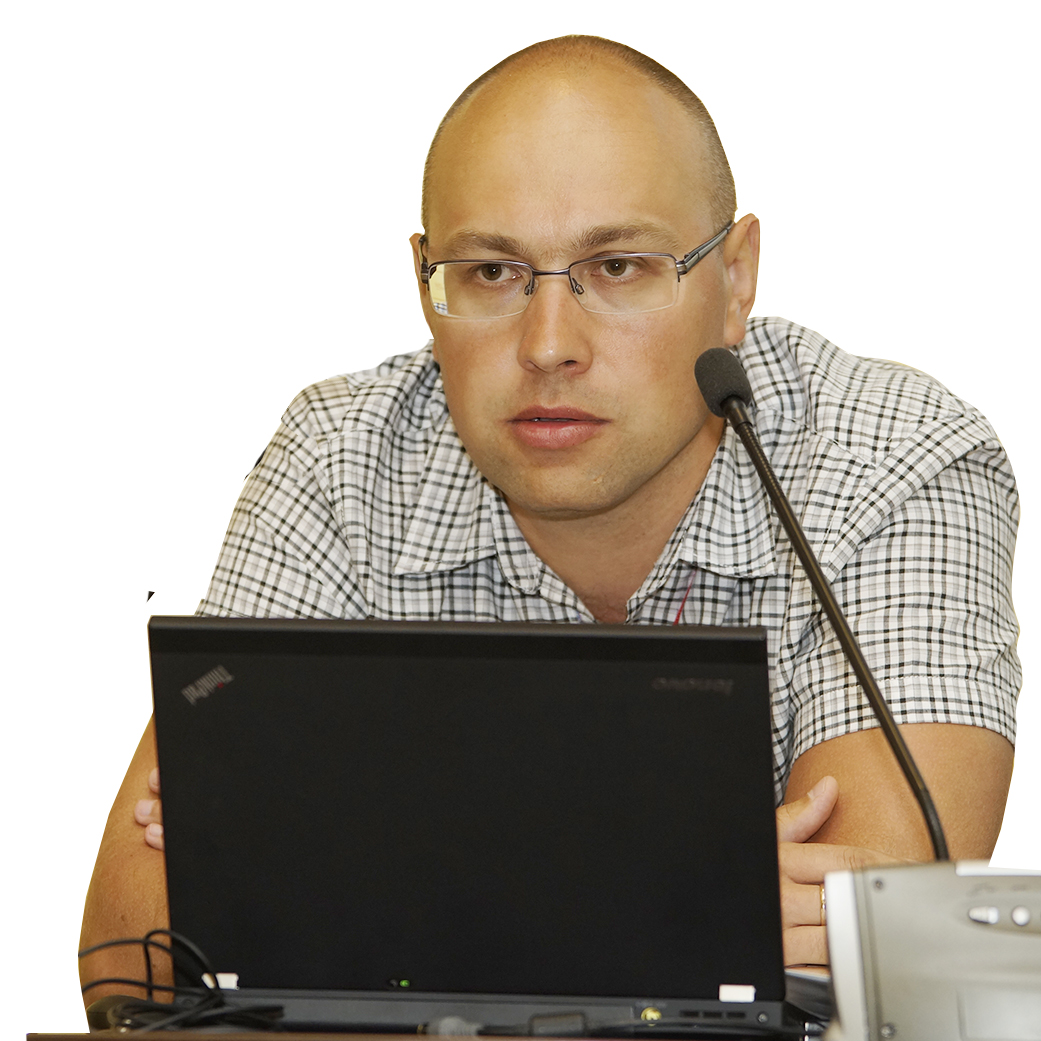
Рассмотрим на конкретном примере, работа в новой системе выглядит со стороны сотрудника производства. Например, приходит приемка сырья — палет замороженного мяса. Пользователь выбирает наименование, вводит дату поступления партии и вес (весы подключены к ИС). Одновременно со взвешиванием производится фотосъемка с weв-камеры — и сразу же печатается паспорт с номером серии. Каждая палета получает свой номер, штрих-код, указание места хранения, на основе которого водитель электрокара повезет ее в определенное место на складе. Конечно, для реализации такой системы потребовались и соответствующие технические средства: промышленные компьютеры, принтеры этикеток, дополнительные принтеры, весы.
«Мы стремились использовать типовые механизмы, заложенные в системе, — поясняет Евгений Голубцов, — чтобы сохранить ее целостность, упростить процесс обновления системы и переход на новые формы регламентированной отчетности. Стояла задача не нарушить типовую конфигурацию, и мы ее выполнили. Сейчас система находится на технической поддержке у «Абсолют Софт», проводятся ее регламентные обновления».
Специализированные АРМ
В системе создано несколько типов универсальных АРМ: «Отвесы», «Термообработка», «Подбор», «Маршрутизация доставки».
На АРМ «Отвес» обрабатывается количество материала, одновременно предназначенного к передаче на следующий этап производства. Для мясного производства важно точно знать вес продукта на всех этапах обработки, своевременно передавать продукцию по стадиям обработки. Оператор регистрирует в системе колбасную раму, на которой висят куски мяса, затем печатает паспорт и прикрепляет его на раму (или на стопку ящиков или палету). Вся эта операция передачи получила название «Отвес» и имеет свой уникальный номер. Номера операций связаны между собой.
Интерфейс, в котором работает оператор настраиваемый: например, в правой части может быть изображение оборудования и оператор может удобно указать оборудование, на котором производились операции. «Мы разработали универсально настраиваемые и «дружелюбные» АРМ, которые стоят на более чем 25-ти контрольных точках, — отмечает Евгений Голубцов. — Формы открываются у пользователя и имеют достаточно простой интерфейс. Входя по паролю, пользователь видит всего две кнопки: одной он открывает журнал, второй создает новый документ. Система сама ведет пользователя по определенному маршруту. Транзакции, создаваемые этими АРМ, стали основой для регламентных документов.
Информация из АРМ используется для составления отчетов — по сотрудникам, по сменам, по бригадам. Причем все эти операции идут в режиме онлайн. Любой сотрудник, в соответствии с его правами доступа, может сформировать в любой промежуток времени отчет: сколько продукции выпустил цех, на каком участке и на каком оборудовании.
Идентификация тары. «Мясное производство в силу своей специфики затрудняет нанесение идентификаторов, —поясняет Евгений Голубцов, — будь то бирки или даже RFID-метки. Высокая влажность, обработка в термокамерах, нагар приводят к тому, что бирки покрываются копотью, а RFID-метки выходят из строя из-за температуры. При этом пищевые регламенты все равно обязывают иметь понятную маркировку изготавливаемого сырья на каждом переделе. Эту проблему мы решили за счет интеграции информации о таре в серийный номер паспорта продукта, а для идентификации тары мы придумали форму «тарный калькулятор».
Работает это следующим образом: для вычисления веса нетто выбирается тара. Это универсально настраиваемая форма, в каждом подразделении настраиваются определенные кнопки в зависимости от того, какая тара в них используется, причем с уже предвыбранным весом. Большинство видов тары имеют свой фиксированный вес, в отличие от колбасной рамы, которая периодически находится в ремонте, и колбасной тележки, у которой заменяются колеса. Для учета эти особенностей введена обработка «идентификация тары», где вывешивается на небольшой срок ярлык с уникальным кодом, по которому определяется вес. Если такой ярлык есть, оператор сканирует тару и получает вес нетто, который тут же программно «прикрепляется» к номеру серии (партии).
На всех этапах обработки продукция движется по партиям. Для производственного учета ввели бирки на полутушах, на рамах с мясом, на тележках с мясным фаршем, на раме с готовой продукцией, на упакованной продукции на складе готовой продукции.
Паспорт рамы выполняет свою миссию только до определенного момента, затем заменяется и печатается новый. Там, где продукция проходит термообработку, используются такие же бирки, только пластиковые, чтобы они не промокали.
На АРМ «Термообработка» идет контроль процесса термообработки. После выхода продукции с термообработки осуществляется контроль: когда та или другая рама с сырьем прошла термообработку. Монитор АРМ показывает выбор камеры, в которой будет производиться варка или копчение, время входа и выхода рамы из камеры и телеметрия — время операций. После копчения идет охлаждение, когда колбасная продукция должна остыть и не потерять в своем весе. Монитор показывает оператору, когда пора забирать продукцию. Тот входит в камеру, выкатывает рамы с продукцией, сканирует, регистрирует продукцию и передает ее в следующее подразделение.
На АРМ «Подбор» производится сборка заказа клиента и этикетировка продукции. Сейчас от торговых сетей на «Ремит» поступает большой объем требований, причем не только по договорным условиям, но и по логистике, — это вложенности, допуски, типы тары, штрих-коды и даже индивидуальная цена клиента на полке магазина. На заводе порядка 20-ти шаблонов различных клиентов, сделанных под разные организации, а всего номенклатура продаваемой продукции составляет 400—500 позиций. Благодаря прозрачности всего процесса движения продукции на заводе немаркированная продукция (но с паспортами) поступает на склад готовой продукции, пока еще без термочеков с паспортами, которые мы видим в магазинах. И уже непосредственно на рабочих местах операторы под заказ маркируют, взвешивают продукцию. Каждый подбор начинается с открытия сессии — «короба»; по печати суммарной этикетки сессия «короб» закрывается, информация сразу же попадает в расходную накладную.
Оператор видит на экране изображение продукции. Также используются этикетки различной формы и дизайна. На «Ремите» печатаются этикетки с разными логотипами под разные компании, по чьим заказам производится этикетировка.
АРМ «Маршрутизация доставки». У компании 55 собственных автомобилей, плюс к тому наемный транспорт, который тоже занимается развозкой продукции «Ремит», поэтому АРМ «Маршрутизация доставки» была необходима. АРМ обеспечивает распределение продукции по маршрутам доставки, и, если имеется недогруз или перегруз, он тут же в течение 20 минут корректируется.
Результаты проекта
В настоящее время производство, бухгалтерия и отгрузка полностью переведены на работу в системе «1С:ERP Управление предприятием 2.0». Создано 14 рабочих мест по комплектации — этикетированию, а поскольку работа сменная, то всего за терминалами работает 50 комплектовщиков. Новые сотрудники очень быстро — буквально за несколько минут — адаптируются к системе.
Мясная продукция имеет ограниченный срок годности, поэтому особенно важно отслеживать движение продукции в оперативном режиме. Проект позволил решить эту задачу и предотвратить ее усушку и порчу из-за сроков годности. Так как система дает оперативную картину по остаткам, с ними тут же начинается работа. На основных АРМ дополнительно установлены мониторы контроля за партиями продукции: цветовой маркировкой выделяют и сообщают о необходимости переместить партии, в следствие чего потери продукции снизились на 15 %.
Сейчас отдел планирования может в любой момент увидеть полную картину по работе с продукцией: на каких участках какие остатки, что выпустил цех, что находится в камерах, каковы сроки годности, — и тут же быстро произвести корректирующие действия. Один и тот же продукт может выпускаться в разных формах — нарезки, в неупакованном виде, в вакуумной упаковке, в вакуумной упаковке со срезом. И если один и тот же продукт собирается в разные тары, система проконтролирует и этот процесс.
Контроль за работой предприятия идет на самом верхнем уровне — генерального директора. Если возникают какие-то отклонения, по ним сразу принимаются меры и об этом тут же докладывается на планерке генеральному директору.
Перспективы
«Санкции сыграли нам на руку, объемы отгрузки выросли на 15 %, — отмечает Евгений Голубцов. — И конечно же, здесь свою роль сыграла ИС, которая позволила нам гибко адаптироваться под любого клиента». Развитие созданной системы не останавливается, в ближайшее время планируется осуществить запуск следующих подсистем:
— планирование производства по MRP;
— бюджетирование;
— документооборот;
— управление ремонтами.
«Сейчас мы еще учимся работать в системе, и в ее работе пока есть кое-какие шероховатости, — отметил Генеральный директор Анатолий Морозов. — Но при этом у всех сотрудников компании есть ясное ощущение, что то, что мы сделали, — это закладка фундамента нашего бизнеса на многие годы вперед».
Чтобы оставить комментарий пожалуйста Авторизуйтесь