Исторически сложилось, что часть оборудования различной степени изношенности унаследовано ОАО «Останкинский мясоперерабатывающий комбинат» с прошлых времен, часть оборудования — новое, современное, поскольку без него удерживать лидерские позиции, а «Останкино» — лидер по производству и переработке мяса и мясоколбасных изделий, невозможно.
Портрет компании
ОАО «Останкинский мясоперерабатывающий комбинат» — процветающее предприятие, которому принадлежат 17 торговых домов, 26 фирменных магазинов в Москве и одни из самых современных свинокомплексов в стране. На комбинате выпускается 500 тонн продукции в сутки и работает 5500 сотрудников. Все производственные мощности снабжены новейшим немецким и австрийским оборудованием. Совокупность этих факторов позволяет «Останкино» придерживаться международных стандартов в производстве продукции, которая пользуется признанием у покупателей
В конце 2010 года на комбинат пришёл новый технический директор — Клюжев Олег Валерьевич. Ему была поставлена задача — сделать работу технической службы прозрачной с последующей оптимизацией затрат.
Деньги на ремонт оборудования выделялись, но было не понятно, куда они уходят, на какое оборудование? Вкладываются ли они как в бездонную бочку в старое оборудование, которое еле-еле «дышит» между ремонтами? Или в оборудование, которое требует лишь регулярного ухода и обслуживания для своей надёжной и стабильной работы? Какова отдача этих вложений? Для ответов на эти вопросы нужно сначала собрать информацию о том, какие работы производятся с оборудованием, какое время необходимо для проведения работ и какие материалы должны быть использованы.
Были попытки использовать Excel. Но для огромного комбината, на котором исполняется множество процессов, нужен программный продукт (информационная система), позволяющая объединить в себе все подразделения технической службы, службу материально технического снабжения и производственные цеха. При этом система должна быть коммерческим продуктом, т.е. использоваться другими промышленными предприятиями. Кроме того, она должна легко адаптироваться под специфику нашего предприятия. И ещё одно немаловажное условие — компания — разработчик системы должна оперативно предоставлять консультации по вопросам функционала и работы программного продукта.
Выбрали систему «1С:ТОИР Управление техническим обслуживание и ремонтами», разработчик которой компания «Деснол Софт Проджект». Было понятно, что выбрав данный программный продукт, можно снизить влияние человеческого фактора к минимуму, поскольку программа разрабатывается не конкретным человеком, а фирмой. Тем самым при увольнении того или иного сотрудника процесс разработки и консультирования не останавливается. К тому же на комбинате имеются специалисты по программам фирмы «1С», что повышает надёжность эксплуатации системы и её поддержки и позволяет штатными средствами дорабатывать необходимый нам функционал.
Факторы успеха
Сразу можно сказать, что проект выполнен успешно. Успех был достигнут благодаря нескольким факторам. Во-первых, задачу ставил генеральный директор Попов Михаил Владимирович, который выступил в роли заказчика. Во-вторых, курировал проект технический директор — Клюжев Олег Валерьевич. В-третьих, проверка работоспособности системы проводилась на рабочих местах. Например, если работник научился строить в системе графики или распечатывать наряды, то работа принималась. Если же нет, выясняли, почему. Это могли быть какие-то недоработки в системе, или человеку нужно развить свои навыки и умения работы на компьютере.
Был принят индивидуальный подход к обучению сотрудников. Учить приходилось каждого и по-разному. Групповые методы обучения не подходили. Когда человеку уже 40 лет и больше, ему некомфортно, не то, что стыдно, но он испытывает неловкость: пришли новые антикризисные менеджеры, начинают учить, «мы здесь гайки крутим, а нас заставляют на компьютере кнопки нажимать». Работали с людьми жестко, но с уважением. Семен Семенович, давай, посмотрим методичку вместе. Нажимай кнопку — нажал. О, получилось! Переворачивай страницу, читай, нажимай. Снова получилось! Надо же, работает! И так с каждым. Каждого надо было обучить, к каждому найти подход. Кроме того, система со всей хранимой в ней информацией — это постоянный контроль, который людям не нравится. Конечно, можно работать по принципу «не умеешь, научим, не хочешь, заставим» или же «не хочешь, тогда нам с тобой не по пути». И только благодаря индивидуальному подходу к каждому работнику, сохранили кадры, которые так нужны предприятию.
Сбор информации
Работу мы начали с описания операций, проводимых с конкретным оборудованием, т.е «перекладывали» знания людей из ежедневников, голов в систему. Структурировали операции, определяли их последовательность, продолжительность при обслуживании того или иного оборудования, разрабатывали нормы. Процесс трудный, люди не готовы были делиться своим опытом, возмущались: «Я работаю уже столько лет, и сам всё знаю». Но мы знали, когда сформированы регламенты работ, технологические карты, в которых указаны перечень операций, их последовательность и время выполнения, и ещё перечень запчастей, которые нужно заменить, то автоматически снижается влияние человеческого фактора на качество работ и уменьшается время ввода нового сотрудника в производственный процесс.
Учёт материалов
Материалы — один из ключевых элементов, поскольку из них складываются бюджеты. Начали вести учет материалов на ремонты, то есть, какие материалы по факту израсходованы на тот или иной объект. Мы понимали, что план можно будет сформировать чуть позже, а сейчас нужно собрать фактические данные. Допустим, сломалось оборудование, надо сменить подшипник. Со склада товарно-материальных ценностей рабочий берёт нужную запасную часть, проводит ремонт, и в системе указывает, что данный подшипник ушел на ремонт такого-то оборудования.
Комбинат работает по факту износа. Поэтому задача менеджмента — максимально использовать ресурс инструмента (оборудования). Можно что-то менять, например, через каждые 300 часов работы, но если всё работает нормально и исправно, зачем? Сломалось — меняем. Поэтому первый отчет, который мы построили в информационной системе, — отчёт о фактических затратах на ремонт (рис.1). Всё получилось, наши работники справились с задачей и зафиксировали в системе информацию о проведенных фактических ремонтах и использованных материалах.
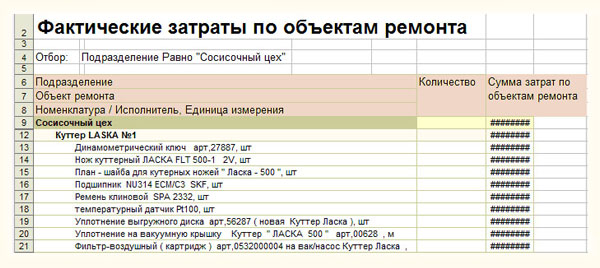
Более того, мы сумели решить ещё одну важную задачу. Так, ремонтно-техническая служба состоит из нескольких подразделений. И в каждом из них одно и то же изделие называли по-разному. В то же время поставщики это же изделие могли называть по-своему. Получалось, что, к примеру, резиновое уплотнение с железным профилем кто-то называл манжетой, кто-то резиновым кольцом, кто-то ещё как-то, а на складе — полная неразбериха.
Когда поставили систему, то привели справочник товарно-материальных ценностей в соответствие с технической документацией. Теперь все работают с одним названием, и всем понятно, что как называется. Даже на начальном этапе система позволила навести порядок. В результате ведение товарно-материальных ценностей (ТМЦ) в системе позволило нам увидеть, какие запчасти закупаются и остаются на складе, а каких всегда не хватает. Теперь при закупке ТМЦ анализируются их текущий остаток, статистика расхода и утвержденная норма (количество, которое должно быть на складе для проведения аварийных ремонтов). На основании статистики расхода ТМЦ стали формировать бюджет подразделений.
Формирование системы обслуживания и планов
Прописанные операции и их периодичность легли в основу графиков планово-предупредительных ремонтов (ППР) и обслуживания (рис.2). Теперь каждый мастер ежедневно выдает слесарю наряд на работу, в котором расписано, где, по какому оборудованию, что надо сделать — протереть, смазать, проверить. Например, если гайки ослабли, то подтянуть или сделать ещё что-то.
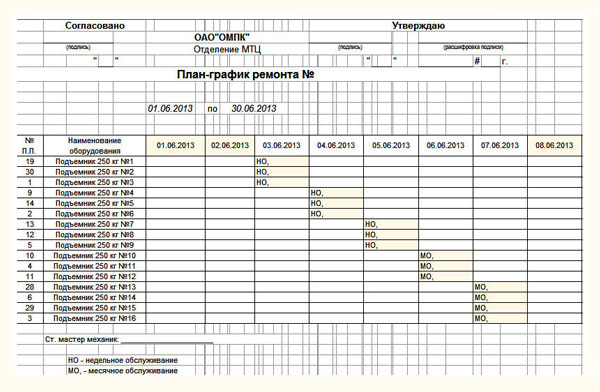
Рис. 2. График планово-предупредительных ремонтов и обслуживания
И сегодня, допустим, пришел новый слесарь, получил наряд (рис. 3) на еженедельное обслуживание, например, смазку, и он видит, что и как должен делать, поскольку есть документ «Операция смазка». И он всё сделает правильно: смажет, проверит и, главное, за это распишется. Если же что-то случится, то поднимаем наряд на работы, проверяем, кто, что делал, чья подпись стоит — элемент контроля.
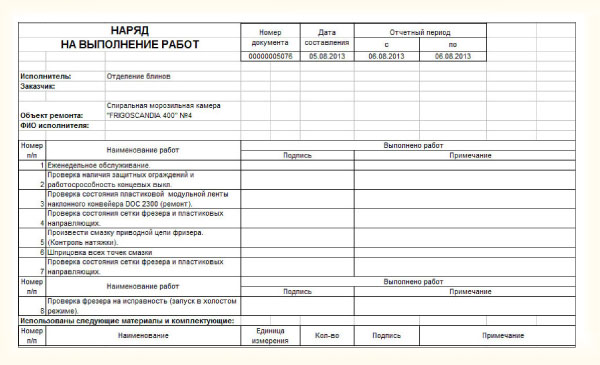
Рис. 3. Наряд на выполнение работ
Система контроля
Хотя информационная система предназначена для решения задач технического обслуживания и ремонтов оборудования, с нею на комбинате работают и производственники. Это сделано для обеспечения контроля работы оборудования. Так, если оборудование сломалось, то работник производственного подразделения должен просто указать, что в такое-то время оборудование не работает, сломалось или остановилось, не указывая никаких причин. Потому что задача основного производственника, оператора линии — делать колбасу, пельмени, а не заниматься анализом, что сломалось, почему остановилось. Информация фиксируется в системе, техническая служба видит её, оперативно выявляет причину и тут же привлекает нужных специалистов. В системе видно, какое оборудование сломалось, какая служба работала, что сделала (рис. 4).
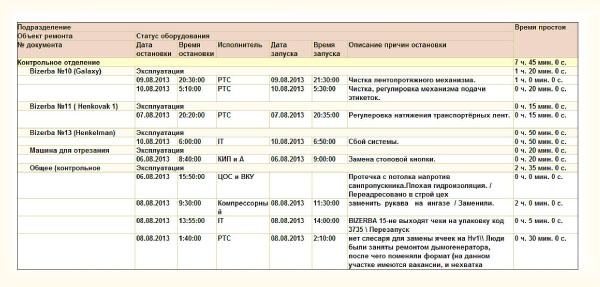
Если оборудование не работает, производство простаивает, продукция не выпускается. Поэтому техническая служба стремится максимально быстро ликвидировать поломку. Таким образом, в системе имеются два фактора анализа (см. подробнее, как провести план-фактный анализ). Первый — заявки и информация о поломках и простоях со стороны производственников, и второй — планы технического обслуживания.
Коллеги из «Деснол Софт Проджект» помогли создать в системе инструмент, который позволяет свести обе «картинки» в единую и увидеть график, когда оборудование должно обслуживаться, фактическое исполнение, и когда оно остановилось (рис. 5). Тут уже можно прорабатывать варианты, что нужно делать, то ли доработать операции обслуживания, то ли изменить его частоту, то ли дополнительно включить ещё операцию, например, не только смазать, но и проверить другой узел, другой элемент.
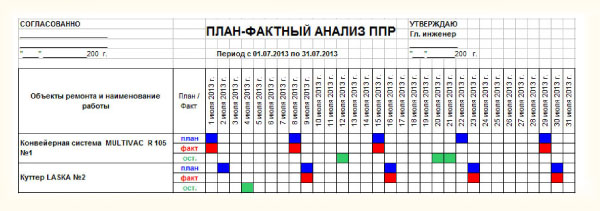
Система позволяет контролировать, анализировать, делать выводы, чтобы оборудование меньше и реже ломалось. Не ломаться вообще оно не может. Но его остановки не должны приводить к недовыпуску продукции. Внедрение системы и её использование позволили решить задачу не столько проведения планово-предупредительных ремонтов, сколько обеспечения стабильной и надёжной работы оборудования и всего производства по выпуску продукции.
Управление человеческими ресурсами.
Решили ещё одну задачу — оптимизация работы персонала. Так, когда мы прописывали операции, то одновременно указывали время, которое нужно для их выполнения. На основании графиков ППР рассчитывается плановая занятость ремонтников (рис. 6). В то же время работники подразделений работают по своему графику, из которых и складываются часы работы подразделения (рис.7).
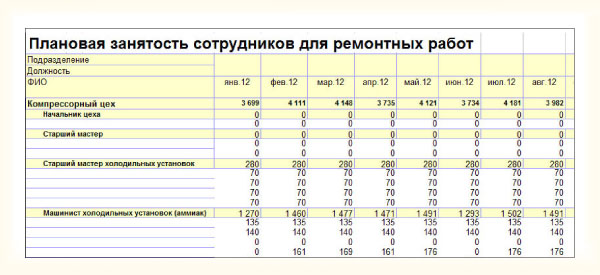
Рис.6. Плановая занятость сотрудников для ремонтных работ
Рис.7. Часы работы подразделения
Сравнивая время, необходимое для проведения ППР, с графиком работы подразделения и учитывая статистику времени на устранения аварийных ремонтов, мы определили, на каких участках есть дефицит, а где избыток сотрудников (рис. 8). Система позволила уйти от эмоциональной составляющей. Теперь ничего не надо никому доказывать, всё видно, кто, что делает, сколько занят, нужно ли кому-то перенести отпуск, выпавший на запланированный ремонт, или распределить сотрудников внутри подразделений.
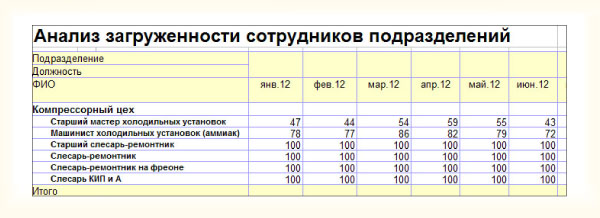
Рис.8. Анализ загруженности сотрудников подразделений
В общем случае, система позволяет даже делать выбор, нужен ли штатный работник, который работает, например, только три часа в месяц, или периодически привлекать таких специалистов со стороны. В системе появился элемент управления персоналом, и её можно рассматривать сегодня как инструмент комплексного управления не только материальными ценностями и ремонтом, но также и персоналом.
Сегодня мы имеем инструмент комплексного управления как персоналом, так и финансами. С внедрением системы «1С:ТОИР Управление техническим обслуживание и ремонтами» работа технической службы стала полностью прозрачна. Видно, какое оборудование чаще ломается, какие средства на него потрачены, чем занят персонал. Руководители структурных подразделений начали более эффективно использовать денежные средства. Они видят в системе, какие работы по обслуживанию планируются, какие для этого нужны материалы и средства.
Чтобы оставить комментарий пожалуйста Авторизуйтесь