Ситуация до старта проекта
Вследствие кризиса два года назад с рынка ушел главный конкурент «Цикла» — китайские производители. При этом на предприятии в 2016 году ввели новые производственные мощности. Это привело к росту продаж и объемов производства. Строительство нового производственного и складского корпусов позволило увеличить объемы производства в 2,5 раза. См. также про описание бизнес-процессов.
Однако, в компании перестали справляться с оперативным планированием производства продукции, какие-то поставки срывали, не знали точно, где и что лежит на складах. «Требовалось собрать воедино и усовершенствовать весь производственный функционал, а также снизить ручной труд по планированию и повысить управляемость производством», — рассказывает Ирина Хлупнова, руководитель ИТ-проектов предприятия «Цикл».
Проблема осложнялась тем, что до внедрения «1С: ERP Управление предприятием 2» на заводе использовалась система «1С: Управление производственным предприятием 8». Она была очень сильно переработана, содержала в себе много нетипового функционала, в том числе функционала планирования производства, который, по сути, заключался в ручном планировании. Ручным составлением планов, сменных заданий занимался отдел планирования. При этом в программе практически не было учета хода производства — он был номинальным, по факту произведенной продукции на нее просто списывались материалы, и раз в месяц проводились инвентаризации, по которым выверялись остатки.
Владелец компании и топ-менеджмент поставили следующие задачи:
- сократить незавершенное производство;
- оптимизировать производственные запасы;
- ускорить выпуск готовой продукции;
- обеспечить равномерную нагрузку на производство.
Решить эти задачи на старой системе было сложно, поэтому, выбрали новую — «1С: ERP Управляем предприятием» (на тот момент это была ее бета-версия).
Выбор поставщика ИТ-услуг
«Когда в 2015 году было принято решение о старте проекта, первая задача, которую мы решали — какими силами будем реализовывать проект: самостоятельно или привлекать поставщика со стороны», — вспоминает Ирина Хлупнова. — В итоге решили приглашать поставщиков ИТ-услуг, поскольку, во- первых, они дадут объективную экспертную оценку, которая будет ориентировать предприятие в правильном направлении. И, во-вторых, разъяснят, как решение «ложится» на систему управления производством.
Критерии выбора внешнего поставщика ИТ-услуг были следующими:
- опыт работы с производственными предприятиями;
- проектный подход, необходим был партнер, который будет способен совместно с ними сделать проект «под ключ» — составлять функциональное описание требований, разрабатывать техническое описание, причем так, чтобы менеджерам и пользователям было все понятно;
- стоимость услуг.
Всем этим критериям хорошо отвечала компания «ИТРП» и выбор в ее пользу был сделан достаточно быстро.
Руководство проектом и этапы
Проект получил поддержку на самом высоком уровне. Основные двигатели проекта — собственник компании и коммерческий директор, который выступал куратором.
Активное участие в работе принимали начальник планового отдела и начальник технологического бюро. «Эти два менеджера готовили вместе со мной функциональную модель, — отмечает Ирина Хлупнова, — вместе с ними мы описывали все математические модели наших изделий, чтобы заложить их в систему и смоделировать. Объем работы был очень большой».
Проект состоял из четырех этапов.
- Обследование предприятия. На этом этапе проектная команда общалась со всеми менеджерами по производственным и смежным бизнес-процессам.
- Составление функциональной модели предприятия и ее согласование со всеми менеджерами.
- Разработка автоматизированных рабочих мест отдела планирования и производственного подразделения.
- Обучение сотрудников и опытная эксплуатация системы.
На предприятии постоянно находился и беседовал со всеми сотрудниками представитель компании-внедренца. Примерно за месяц была разработана концептуальная модель, согласованы все требования к системе.
В 2016 году предприятие переехало в новые корпуса, и проект был временно приостановлен. «Как только производство в новых корпусах было запущено, мы незамедлительно вернулись к проекту — в мае 2017 года», уточняет Ирина Хлупнова. С 1 июня проект запустили в опытную эксплуатацию.
Во время опытной эксплуатации приходилось работать сутками, ведь и само предприятие работает круглосуточно. Нужно было обучать работников, настраивать систему, выявлять и исправлять все ошибки. В этом принимали участие все менеджеры. «У нас был случай, когда команда внедрения не сразу смогла запустить учет отходов в полном объеме, к этому отнеслись с пониманием, и начальники смен часть информации в систему вводили вручную», — рассказывает Ирина Хлупнова.
Архитектура системы
В системе «1С: ERP Управление предприятием» работают следующие блоки:
- управление продажами;
- управление закупками;
- управление запасами в связке с системой «1С: WMS»;
- планирование продаж и планирование производства;
- планирование закупок; • управление нормативно-справочной информацией;
- расчёт себестоимости;
- управление ремонтами оборудования.
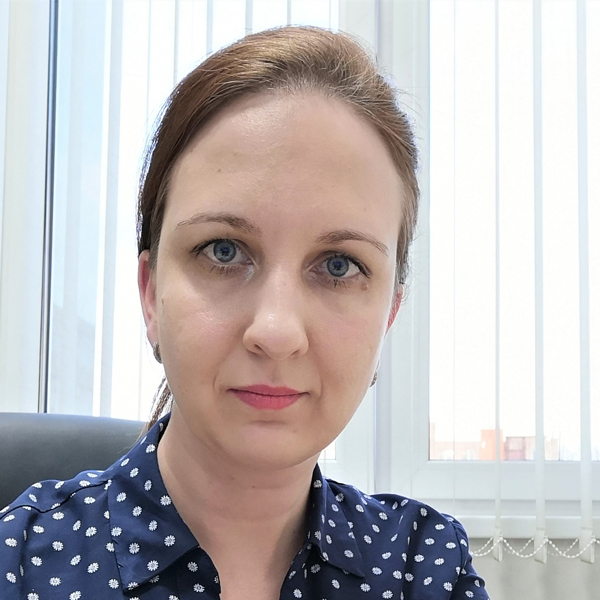
Во время работы над проектом были сделаны некоторые доработки типового решения:
- Реализовано автоматизированное рабочее место (АРМ) операторов, которое стоит на шести терминалах в цеху. Появление первичной информации в системе идет непосредственно от первоисточника — конкретного сотрудника. Каждый выпускающий продукцию работник должен сам отчитаться за то, что он сделал, какие работы выполнил.
- Создано АРМ закрытие смены.
- Введено АРМ формирования расписаний и графиков для планового отдела.
- Разработан документ «План остатков», которым пользуется плановый отдел и отдел продаж.
Общее число пользователей, которые используют систему «1С: ERP Управление предприятием», приближается к 80. В системе работают порядка десяти инженерно-технических работников производства.
Новая методология планирования производства
На предприятии полностью поменяли систему планирования производства, причем не только в части выполнения расчетов, но и в части самой методологии. До внедрения системы «1С: ERP Управление предприятием» планирование сводилось к «ручному» прогнозу: что нам нужно произвести, чтобы выполнить планы продаж. Это приводило к затовариванию складов, к излишкам полуфабрикатов, которые негде было хранить.
С внедрением «1С: ERP Управляем предприятием» перешли на методологию планирования под страховой запас. Причем, как под страховой запас готовой продукции, так и под страховой запас полуфабрикатов собственного производства.
На предприятии ограниченный парк оборудования: порядка 45 термопластических станков, на которых выпускается 700–800 позиций деталей, которые нужно периодически переставлять и дозагружать оборудование. И требуется очень тонкая балансировка оборудования, чтобы выпустить всю ту линейку номенклатуры, которая продается в течение одного сезона. Эту балансировку решено было выполнять не на этапе оперативного планирования и расчета внутрицеховых планов, а на этапе объемного планирования производства продукции. Был разработан документ «План остатков», который позволяет управлять уровнем страховых запасов в зависимости от изменения уровня спроса на продукцию. И, соответственно, именно этим документом выравнивается и балансируется производство, обеспечивается равномерная загрузка оборудования на протяжении всех месяцев сезона. Благодаря «плану остатков» оборудование деталями загружается равномерно.
Для полуфабрикатов собственного производства выбрана экспертная оценка уровня страховых запасов, но и её считали в зависимости от уровня страховых запасов готовой продукции. Обеспечиваются запасы, которые позволяют работать два дня без сбоев. Как только двухдневный запас начинает заканчиваться, система сигнализирует о необходимости пополнения.
«Новая методология планирования очень хорошо себя показала в промышленной эксплуатации. Благодаря ей мы избавились от множества проблем: от перезатоваривания складов и высоких запасов. И, что очень важно, мы получили управляемость и гибкость при производстве — теперь при переходе на продукцию к новому сезону мы не имеем массы полуфабрикатов, которые у нас накапливались прежде», — разъясняет Ирина Хлупнова.
Учёт материалов и полуфабрикатов
«Исторически учет материалов и полуфабрикатов вёлся по факту выпуска изделий, все списания на расход оформлялись по нормам, без учета отклонений от реального потребления. Постоянно выполнялись корректировки остатков, что требовало дополнительных трудозатрат на проведение инвентаризаций. Сейчас мы перешли к нормальному учету всех единиц нашей продукции в режиме реального времени в системе класса ERP. Это было нелегко, к этому не привыкли, сложности есть и до сих пор. Но, по крайней мере, сейчас на предприятии можно уверенно говорить — где, и сколько чего у него есть», — отмечает Ирина Хлупнова.
Успех проекта
Успех проекта связан с заинтересованностью менеджерского состава и поддержкой руководства. Если бы я столкнулась с сопротивлением менеджеров, мы вряд ли получили бы такие результаты. Кроме того, надо помнить, что исполнители будут всегда сопротивляться изменениям. Для них автоматизированная система — это изменение обязанностей и увеличение прозрачности их работы, а такое понравится не каждому. Необходимо быть к этому готовым и иметь план по внедрению изменений в работу конечных исполнителей.Ирина Хлупнова, руководитель ИТ — проектов компании «Цикл»
Результаты
«В результате мы смогли повысить управляемость и запасами и производством в целом, повысили точность и эффективность как планирования производства, так и учета продукции, материалов и полуфабрикатов», — резюмирует Ирина Хлупнова. С помощью системы маркируется вся выпускаемая продукция. Маркировка содержит информацию о том, кто когда, в каком количестве выпустил продукцию. Это позволяет найти работника, допустившего брак при получении рекламации от клиента.
Количественные результаты проекта:
- снижение запасов собственного производства на складах — 30%;
- рост эффективности труда ИТР и служащих — 20%;
- повышение точности планирования — 60%;
- снижение уровня незавершенного производства —20%;
- сокращение времени на планирование — 60%;
- повышение точности учета хода производства — не менее 80%.
Полная окупаемость проекта будет понятна, когда на предприятии внедрят функционал финансового планирования и бюджетирования. Тогда можно будет посчитать, как с помощью системы фирма «Цикл» экономит деньги. На сегодняшний момент, за счет сокращения складских запасов и повышения точности учета хода производства, проект окупился на 40%, считает Ирина Хлупнова.
«Все особенности предприятия, например, сезонность, планирование остатков готовой продукции по полуфабрикатам, построены на базе типового функционала, собственных доработок мы практически не делали. Поэтому тиражировать решение на предприятия, сходные с нашим, труда не составит», — полагает Ирина Хлупнова.
Планы и перспективы
Использовать систему «1С: ERP Управление предприятием» для регламентированного учета на предприятии пока не планируют. В ближайших планах развитие финансового планирования и бюджетирования. Еще одна задача — перейти на версию «1С: ERP Управление предприятием 2.4», пока работа идет на версии 1С: ERP Управление предприятием 2.1«, на которой сделан проект.
Дальние перспективы — автоматизировать на системы «1С: ERP Управление предприятием» регламентированный учет. Тогда можно будет получать из этой системы бухгалтерский баланс, чтобы связать бухгалтерию с управленческим учетом в режиме онлайн. Есть планы интеграции «1С: ERP Управляем предприятием» с системой управления продажами на базе «1С: Битрикс24».
Чтобы оставить комментарий пожалуйста Авторизуйтесь